Aluminium composite panels
Aluminum composite panels (ACP) are façade panels with thin aluminum layers attached on both sides. The panels are reinforced internally with thermoplastic polyethylene core or a mineral fire-resistant layer.
Decorative finishing panels can be used in both outdoor and indoor environments.
Warranty on coating up to 40 years
Easy to clean
Resistant to UV, moisture and chemicals
Decorative finishing panels for use in both outdoor and indoor environments.
Aluminum composite panels are facade finishing panels with a thin aluminum layer attached on both sides.
Between the layers is a mineral core that prevents the spread of fire, meeting fire classification standards of B-s1,d0 or class A2 (EN 13501-1 standard).
Our range of composite panels includes:
The outer layer is typically coated with a highly durable PVDF paint, anodization, or another type of finish.
It is also possible to produce so-called chameleon surfaces, where the panels are coated with multi-layer chameleon paint that changes color depending on the viewing angle.
Advantages of aluminum composite panels
Aluminum composite
Properties of composite panels
Aluminum composite panel is an excellent decorative material for both interior and exterior applications.
Weight
Lightweight design reduces the processing time of composite panels and simplifies as well as speeds up their installation on-site.
Compared to traditional metal panels, they are 30–50% lighter, resulting in less load on the supporting structural elements.
Weather-resistant
Surface coating warranty up to 40 years. Durable against UV radiation, moisture, and exposure to various chemicals, salts, and other substances.
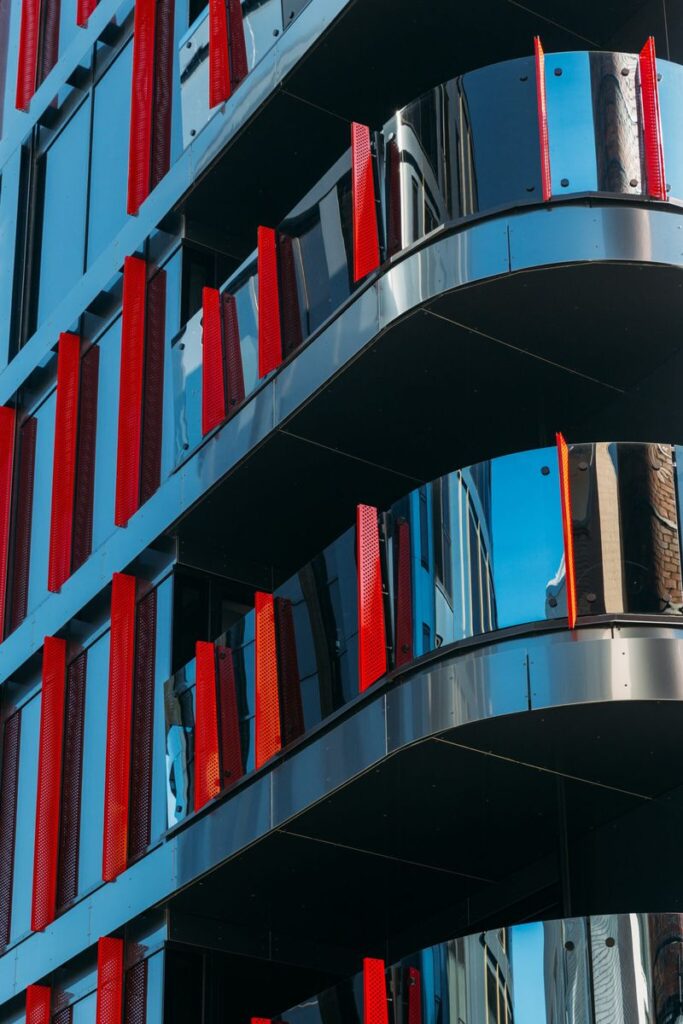
Fire safety
Panels are available in both Bs1,d0 and A2 fire classification ratings.
For high fire-risk areas, composite panels with a special fire-resistant core material are available.
Shape retention and maintenance
Composite panels offer excellent shape stability – they do not warp and remain completely flat and smooth.
The outer coating of the sheets does not crack when bent, and the panels do not deform under windy or sunny conditions.
After several years of use, the panels can be easily cleaned with neutral detergent and water.
Color options
Aluminum composite panels can be produced in a wide range of colors. Additionally, panels with chameleon surfaces are available, coated with multi-layer chameleon paint that changes color depending on the viewing angle.
We also offer composite panels with finishes in copper, brass, patinated copper, stainless steel, and zinc.
Choose the perfect color and gather inspiration for your façade.
Alucoil, a leading manufacturer of aluminum composite panels, has created an online platform where you can explore Alucoil projects from around the world and discover material and color solutions: https://alucoildesign.com/
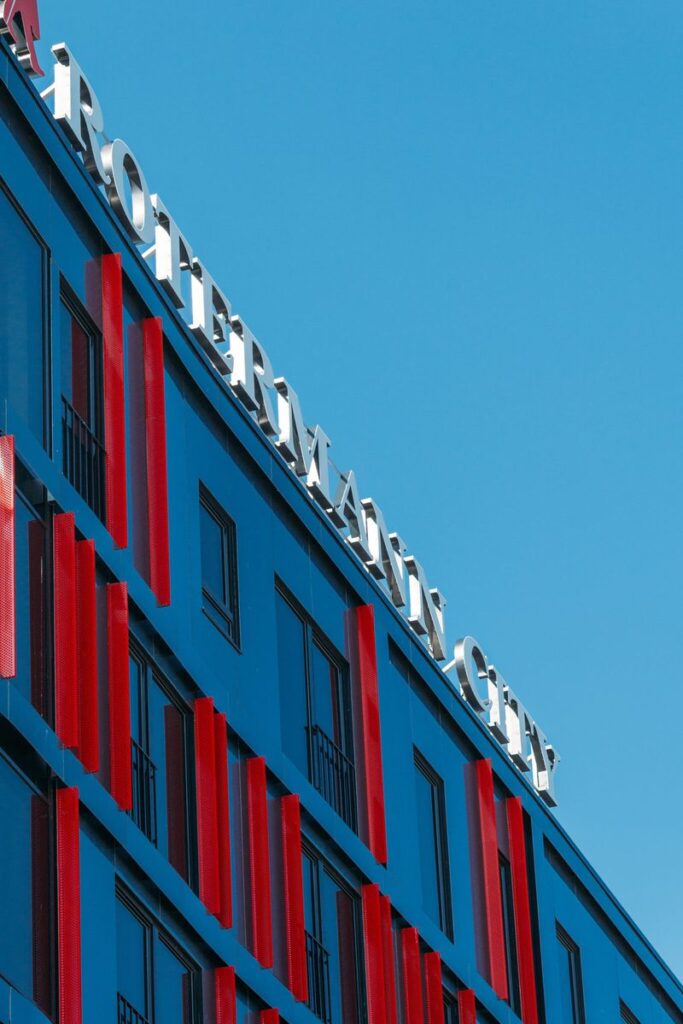
Exclusive modern buildings with a unique touch
Rotermann city features exclusive new buildings, where we have proudly contributed to the execution. Behind the copper-gold elements lie Alucoil aluminum composite panels, used as façade materials for the buildings. The unique color scheme of the façades catches the eye of passersby, both in the darkness and under the bright daylight sun.
Color: “Alucoil Sparkling Antracite Grey“.
The golden and red buildings were completed in 2017
Main Contractor: Nordecon AS
Frequently Asked Questions
Request a Quote
We assist in selecting and designing the appropriate subframe and fastening solution according to the preferences of the building’s architect, client, and structural engineer.